More Stiffness with Less Fiber: End-to-End Fiber Path Optimization for 3D-Printed Composites
Proc. ACM Symposium on Computational Fabrication, October 2023
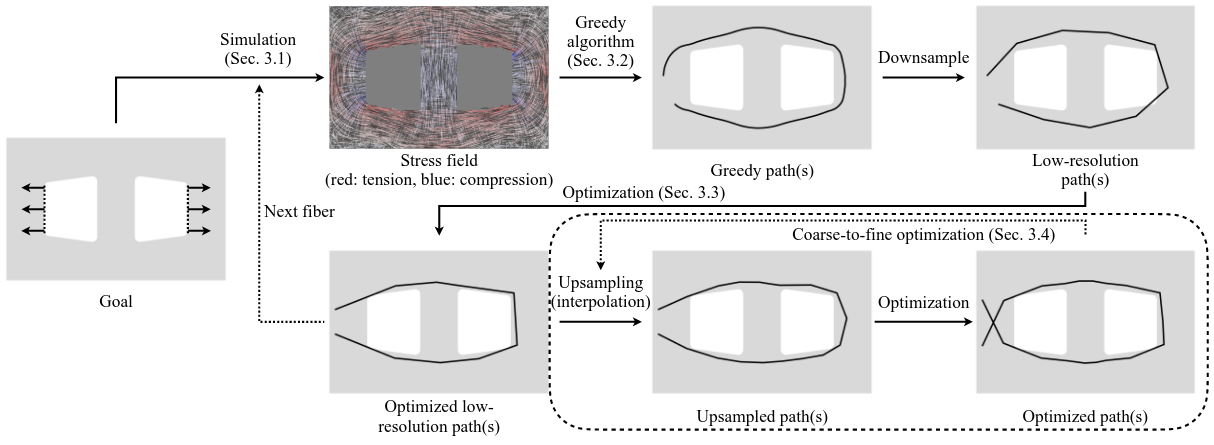
We repeatedly use the finite element method to calculate the stress field of the object, extract a new fiber path
by greedily “walking” on the stress field, optimize the downsampled fiber path with an objective function designed to
maximize stiffness and regularize fiber paths to be manufacturable, and finally upsample and optimize all the fiber paths
several times to perform coarse-to-fine optimization.
Abstract
In 3D printing, stiff fibers (e.g., carbon fiber) can reinforce thermoplastic polymers with limited stiffness. However, existing commercial digital manufacturing software only provides a few simple fiber
layout algorithms, which solely use the geometry of the shape. In
this work, we build an automated fiber path planning algorithm
that maximizes the stiffness of a 3D print given specified external
loads. We formalize this as an optimization problem: an objective
function is designed to measure the stiffness of the object while
regularizing certain properties of fiber paths (e.g., smoothness). To
initialize each fiber path, we use finite element analysis to calculate
the stress field on the object and greedily “walk” in the direction
of the stress field. We then apply a gradient-based optimization
algorithm that uses the adjoint method to calculate the gradient of
stiffness with respect to fiber layout. We compare our approach, in
both simulation and real-world experiments, to three baselines: (1)
concentric fiber rings generated by Eiger, a leading digital manufacturing software package developed by Markforged, (2) greedy
extraction on the simulated stress field (i.e., our method without
optimization), and (3) the greedy algorithm on a fiber orientation
field calculated by smoothing the simulated stress fields. The results show that objects with fiber paths generated by our algorithm
achieve greater stiffness while using less fiber than the baselines—
our algorithm improves the Pareto frontier of object stiffness as
a function of fiber usage. Ablation studies show that the smoothing regularizer is needed for feasible fiber paths and stability of
optimization, and multi-resolution optimization helps reduce the
running time compared to single-resolution optimization
Paper
Links
- This publication on arXiv
Citation
Xingyuan Sun, Geoffrey Roeder, Tianju Xue, Ryan P. Adams, and Szymon Rusinkiewicz.
"More Stiffness with Less Fiber: End-to-End Fiber Path Optimization for 3D-Printed Composites."
Proc. ACM Symposium on Computational Fabrication, October 2023.
BibTeX
@inproceedings{Sun:2023:MSW, author = "Xingyuan Sun and Geoffrey Roeder and Tianju Xue and Ryan P. Adams and Szymon Rusinkiewicz", title = "More Stiffness with Less Fiber: End-to-End Fiber Path Optimization for {3D}-Printed Composites", booktitle = "Proc. ACM Symposium on Computational Fabrication", year = "2023", month = oct }